In der optischen Inspektion werden zunehmend Analysen im dreidimensionalen Bereich durchgeführt. Im Folgenden werden optische 3D-Technologien mit Beispielen vorgestellt und es wird auf ihre Vor- und Nachteile eingegangen.
Time-of-Flight
Es ist eine naheliegende Idee, ein Radarsystem mit Licht (Lidar) aufzubauen: Man sendet einen Lichtimpuls aus, dieser wird von einem Objekt reflektiert und das reflektierte Licht wird von einer Kamera aufgenommen. Aus der Zeitdifferenz zwischen Aussenden und Empfangen des Lichtimpulses kann man dann die Entfernung des Objekts berechnen. Wegen der hohen Lichtgeschwindigkeit erhält man so aber nur sehr ungenaue Werte, die noch dazu durch das Umgebungslicht gestört werden.
Für die Laufzeitmessung (Time-of-Flight, ToF) verwendet man daher keine Lichtimpulse, sondern in der Lichtintensität moduliertes, kontinuierliches Infrarotlicht. Die Kamera empfängt das reflektierte Licht und kann, da ja die Modulationsfrequenz bekannt ist, störendes Umgebungslicht ausblenden. Die Entfernung ergibt sich nun aus der Phasenverschiebung zwischen dem ausgesendeten Licht und dem empfangenen Licht. Die Entfernungsauflösung ist auf einige Millimeter beschränkt. Prinzipiell können zahlreiche Bilder pro Sekunde aufgenommen werden, aber um das Rauschen zu reduzieren, müssen je nach Präzisionsanspruch einige Bilder aufaddiert werden, was die Bildrate auf ca. 3 pro Sekunde beschränkt.
Abbildung 1 erläutert das Messprinzip. Abbildung 2 zeigt eine ToF-Kamera und Abbildung 3 eine typische industrielle Anwendung. Geeignet ist die Methode zum Zählen, Sortieren und Greifen sowie zur Vollständigkeits- und Typkontrolle.
Abbildung 1: Prinzip von Time-of-Flight (ToF) Kameras
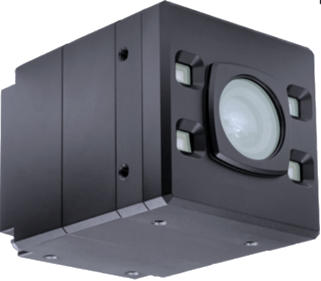
Abbildung 2: Die ToF-Kamera Helios
Abbildung 3: ToF-Bild eines 400 mm durchmessenden Objekts
Vorteile
- Abschattungsfreier Blick von oben auf das Objekt
- Sehr kostengünstige Sensoren, da die Technologie in der Autoindustrie etabliert ist
- Schnelles Verfahren, je nach Anspruch 30 bis 3 Tiefenbilder pro Sekunde
- Großer Messbereich von typisch 0,5 bis 15 Metern
Nachteile
- Geringe Tiefenauflösung von einigen Millimetern
- Beschränkte laterale Auflösung von typisch 640x480 Bildpunkten
- Empfindlich gegen Mehrfachreflexe an benachbarten Objekten oder Wänden
Shape-from-Fokus (SfF)
Dem meist störenden Effekt, dass Objektive nur eine begrenzte Tiefenschärfe aufweisen, lassen sich auch positive Aspekte abgewinnen: Man kann dies für die dreidimensionale Erfassung von Objekten ausnützen. Dazu wird eine Kamera mit einem Objektiv, das eine möglichst geringe Tiefenschärfe aufweist, senkrecht über dem zu vermessenden Objekt auf und ab bewegt. Während der Bewegung werden in bekannten Höhen einige hundert Bilder aufgenommen, in denen man durch Filterverfahren die scharfen Bereiche identifiziert. Anschließend kombiniert man diese jeweils scharfen Bildausschnitte im gesamten Bildstapel zu einem 3D-Bild.
Problematisch ist dabei die Physik der Objektive: Je größer das Blickfeld eines Objektivs ist, umso „besser“ ist seine Tiefenschärfe, was wiederum die Tiefenauflösung beschränkt. Für Objektive mit Blickfeldern in der Größenordnung von einem Millimeter (konfokale Mikroskope) beträgt die Tiefenschärfe nur einige Mikrometer, dementsprechend kann man damit extrem gut aufgelöste 3D-Bilder erzeugen. Für größere Blickfelder sinkt die Auflösung jedoch stark ab.
Anwendungen für konfokale Mikroskope findet man in der Präzisions-Messtechnik und der Qualitätssicherung sehr kleiner Objekte. Größere Systeme werden meist projektspezifisch aus Standard-Komponenten aufgebaut, etwa zur Vermessung von Steckern (Abbildung 4).
Abbildung 4: Prüfung der Pin-Höhen in Steckern mit dem SfS-Sensor von in-situ. Die Tiefenauflösung beträgt 40 µ. Die am Steckerboden erkennbaren Buchstaben sind 0,1 mm hoch.
Vorteile
- Abschattungsfreier Blick von oben auf das Objekt
- Auflösungen bis deutlich unter einem Mikrometer für mikroskopische Systeme
Nachteile
- Marktgängige Sensoren nur im Mikroskop-Bereich (konfokale Mikroskope)
- Lineare Präzisionsachse erforderlich, daher Messzeiten von ca. einer Sekunde
- Hoher Bedarf an Speicherplatz und Rechenkapazität
- Tiefenauflösung bei 20 mm Blickfeld auf 40 µm beschränkt
Weißlicht-Interferometer
Überlagert man zwei Lichtstrahlen, so entstehen aufgrund der Wellennatur des Lichts Interferenzen. Treffen zwei Wellenberge aufeinander, erhält man eine Verstärkung, fällt ein Wellenberg auf ein Tal, so findet Auslöschung statt. Dieser Effekt wird in Interferometern zur hochgenauen Messung kleiner Abstände ausgenützt. Man strahlt dazu mit einem Laser ein Lichtbündel auf einen halbdurchlässigen Spiegel. Der direkte Strahl erreicht das zu erfassende Objekt und wird dort reflektiert, der um 90° abgelenkte Strahl wird durch einen fest montierten Referenzspiegel reflektiert. Beide reflektierte Strahlen durchlaufen dann den halbdurchlässigen Spiegel in umgekehrter Richtung und werden in einer Kamera registriert. Da der Referenzstrahl und der Messstrahl in Abhängigkeit von der Position und der Form des Objekts unterschiedlich lange Wege durchlaufen haben, ergibt sich ein vom Gangunterschieden der beiden Strahlen abhängiges Interferenzmuster. Damit kann man Objekte dreidimensional erfassen. Allerdings wiederholen sich die Interferenzmuster im Abstand von einer halben Wellenlänge, so dass ohne zusätzliche Maßnahmen der Tiefenbereich auf ca. 0,5 µm beschränkt ist.
Abbildung 5: Prinzip eines Interferometers
Eine industrietaugliche Variante, mit der Blickfelder von einigen Quadratzentimetern und Tiefenmessbereiche von einigen Mikrometern bis Zentimetern abgedeckt werden können, ist das Weißlicht-Interferometer. Hier verwendet man Weißlicht, also eine Mischung aus vielen verschiedenen Wellenlängen, das gerade nicht von Lasern stammt. Die Lichtstrahlen sind daher keine kohärenten Wellenzüge, sondern aus einzelnen Wellenpaketen zusammengesetzt. Dies führt dazu, dass man in der Kamera für jeden Punkt des Bildes Intensitätsmaxima erhält, wenn der Weg des Referenzstrahls mit dem Lichtweg des Messstrahls zum jeweiligen Punkt der Objektoberfläche übereinstimmt. Dazu muss allerdings der Spiegel während der 3D-Erfassug des Objekts mit einer Linearachse bewegt werden. Die erzielbare Genauigkeit hängt dabei von der Präzision ab, mit der die Position der Achse bekannt ist, aber auch von der Oberflächenrauigkeit des Materials.
Abbildung 6: Aufnahme einer Münze mit einem Weißlichtinterferometer von Polytec
Vorteile
- Bewährter Industriestandard
- Hohe Messgenauigkeit im Mikrometerbereich
- Keine Abschattung wegen des senkrechten Blicks von oben