Bildverarbeitungssysteme werden oftmals individuell geplant und erstellt. Umso wichtiger ist es, die Abnahme nach einem standardisierten Verfahren durchzuführen. Die Messmittelfähigkeit eines AOIs wird meist nach den Bosch-Verfahren 1, 3 und 7 durchgeführt.
Lastenhefte und Pflichtenhefte
Wird ein automatisches optisches Inspektionssystem (AOI) bestellt, so wird üblicherweise die "vom Auftraggeber festgelegte Gesamtheit der Forderungen an die Lieferungen und Leistungen eines Auftragnehmers innerhalb eines Auftrages" (DIN69901-5) in einem Lastenheft spezifiziert. Wenn der Auftragnehmer das Lastenheft akzeptiert, wird er in einem Pflichtenheft konkretisieren, wie die Anforderungen erfüllt werden sollen. Dies betrifft die vorgesehene Hardware, Software und Dienstleistungen sowie Fähigkeiten und Grenzen des Systems. Dazu gehören insbesondere Normerfüllung, Taktzeiten und Messgenauigkeiten. Dieses Pflichtenheft ist Teil des Angebots bzw. ein Anhang dazu. Auf dieser Grundlage erfolgen dann die Auftragserteilung, die Auftragsannahme und die Abnahme nach Lieferung und erfolgreicher Installation. Dieses Prozedere ist in das Qualitätsmanagement nach ISO 9001 eingebettet, welches die im Unternehmen ablaufenden Prozesse definiert und letztlich die kontinuierliche Optimierung von Prozessen, Produkten und Dienstleistungen zum Ziel hat.
Messmittelfähigkeitsanalyse (MSA)
Ist das AOI installiert, werden zunächst die Rahmenbedingungen geprüft: Sind alle Komponenten inkl. Dokumentation vorhanden, fügt es sich in die Infrastruktur ein, funktionieren die Schnittstellen, sind alle Sicherheitsmaßnahmen getroffen und wirksam, werden die anwendbaren Normen (CE, UAL, EMV- und Maschinenrichtlinien etc.) erfüllt, wird die vereinbarte Taktzeit eingehalten? Danach folgt ein wesentlicher Teil der Abnahme, nämlich die seit ca. 1990 formalisierte, als MSA (Measurement System Analysis) bezeichnete Messmittelfähigkeitsanalyse. Eine allgemeine Norm gibt es dafür nicht, aber in der Automobilindustrie gilt der durch die International Automotive Task Force gesetzte Standard IATF16949 von 2016, der aus der früheren ISO TS 16994 hergeleitet ist. Auf dieser Grundlage werden auch Zertifikate ausgestellt, beispielsweise durch den TÜV. Eine weithin anerkannte Richtlinie für die Durchführung ist die Publikation „Heft 10: Fähigkeit von Mess- und Prüfprozessen“ von Bosch.
Im Bosch-Dokument werden sieben Verfahren beschrieben, auf die auch in diesem Beitrag Bezug genommen wird, insoweit sie für AOIs relevant sind.
Zunächst wird unterschieden, ob es sich bei der Anlage um ein Messmittel handelt oder um ein Prüfmittel. Bei einem Prüfmittel werden diskrete Attribute wie „gut“ und „schlecht“ ermittelt. Diese können direkt aus Mustererkennungs-Verfahren folgen, etwa wenn geprüft wird, ob ein Merkmal (ein bestimmtes Bauteil, ein Code, eine Farbe etc.) „vorhanden“ oder „nicht vorhanden“ ist. Aber auch aus Messungen folgende Attribute wie „zu lang“ oder „zu kurz“ sind möglich. Dabei erfolgt die Klassifizierung anhand von Vergleichen mit ausgewählten Musterteilen, die alle Fehlerarten abdecken müssen.
Bei einem Messmittel werden dagegen kontinuierliche Messgrößen wie Breite, Höhe und Durchmesser etc. mit einer gewissen Messunsicherheit bestimmt und es wird untersucht, ob diese mit den Sollwerten innerhalb vorgegebener Toleranzen übereinstimmen. Dabei sind systematische und zufällige (idealerweise einer Gaußverteilung folgende) Abweichungen der Mess- bzw. Prüfeinrichtung möglich und zu unterscheiden. Damit eine entsprechende statistische Analyse durchgeführt werden kann, müssen hinreichend viele gleichartige Messungen bzw. Prüfungen durchgeführt werden. Die MSA gilt dann ausschließlich für das untersuchte Merkmal. Bei mehreren Merkmalen ist für jedes ein eigener Fähigkeitsnachweis erforderlich. Dabei ist durch exakt (möglichst durch ein zertifiziertes Prüflabor) vermessene Referenzmuster die Rückführbarkeit auf internationale Normen sicherzustellen.
Eine weitere wesentliche Kategorisierung ist, ob die Messergebnisse mit einem Mess- bzw. Prüfwerkzeug (beispielsweise einer Lehre) durch eine Bedienperson ermittelt werden, oder ob eine automatische Messwerterfassung vorliegt. Bei einem AOI ist generell letzteres der Fall.
Die Auswertung erfordert statistische Analysen, wofür man Excel-Tabellen verwenden kann. Vor-zugsweise kommt aber Statistik-Software wie qsSTAT unter Verwendung der ANOVA-Methode zum Einsatz. Damit erhält man auch eine übersichtliche Darstellung mit Grafiken.
Die Bosch-Verfahren
Für automatisch arbeitende AOIs sind die im Folgenden vorgestellten Bosch-Verfahren 1, 3 und 7 relevant.
Verfahren 1: Systematische Messabweichung und Wiederholbarkeit
Mit dem Verfahren 1 werden kontinuierlich messende Systeme geprüft. Zur Durchführung wird ein kalibriertes Normal mindestens n=25 bis n=50 Mal vermessen. Der Referenzwert xm des Normals soll möglichst in der Mitte des Toleranzbereichs T des zu messenden Merkmals liegen. Der Toleranzbereich ist die Differenz zwischen dem oberen zulässigen Grenzwert OGW und dem unteren zulässigen Grenzwert UGW: T= OGW - UGW. Aus den n Einzelmessungen xi wird der Mittelwert x̅ gebildet. Die Abweichungen x̅ - xm des Mittelwerts vom Referenzwert sind ein Maß für die systematischen Abweichungen (Bias), die Standardabweichung s des Mittelwerts ist ein Maß für die zufällige Streuung. Daraus werden die Fähigkeitsindizes Cg und Cgk berechnet.
Die MSA ist positiv, wenn sowohl Cg>1.33 als auch Cgk>1.33 ergibt. Damit diese Forderungen erfüllt werden können, muss die Messunsicherheit des AOI um mindestens den Faktor 10 kleiner sein als der Toleranzbereich. Dies gilt aber auch für den bisweilen als „wahren Wert“ bezeichneten Referenzwert xm, der seinerseits um den Faktor 10 genauer sein muss als die Messunsicherheit MU des AOI. Beträgt beispielsweise die Toleranz ±10 µm, so ist der Toleranzbereich T=20 µm. Man wird also das AOI mit einer Messunsicherheit von mindestens MU=2 µm auslegen. Der Referenzwert sollte dann auf 0,2 µm genau sein. Siehe dazu Abbildung 1. In manchen Fällen stößt man dabei aber auf physikalische oder technische Grenzen, beispielsweise wenn die Oberflächenrauigkeit des Prüfobjekts bereits in der Größenordnung von Mikrometern liegt. Systematische Abweichungen können auch dadurch auftreten, dass Referenzmaße oft mit taktil arbeitenden Koordinatenmessmaschinen ermittelt werden, die jedoch Oberflächenrauigkeiten auf andere Art mitteln als optische Methoden. In der Praxis wird man daher den systematischen Abweichungen durch eine Kalibrierung der Messeinrichtung Rechnung tragen. Zu erwähnen ist nochmals die Bedeutung des Referenzmusters für die Rückführbarkeit auf internationale Normen. Es sollte daher für eine periodische Überprüfung des AOI sorgfältig aufbewahrt werden, um auch die im Qualitätsmanagement festgelegte Stabilität der Messwerte sicher zu stellen. Abbildung 2 zeigt die mit einer Standard-Software erstellte Grafik einer MSA.
Abbildung 1:
Beispielhafte Darstellung des Toleranzbereichs um den Referenzwert xm. Der untere und obere Grenzwert (UGW und OGW) sowie die Messunsicherheit MU und ein Messwert xi sind eingetragen.
Abbildung 2: Ergebnis einer MSA nach Verfahren 1 mit folgenden Daten:
Anzahl der Messungen n=51; Toleranzbereich T=160 µm; Referenz xm=131.8 µm; Mittelwert x̅ =126.2 µm; Standardabweichung s=2.37 µm. Daraus folgen die Fähigkeitsindizes Cg=2.25 und Cgk=1.46.
Verfahren 2 und 3: Wiederhol- und Vergleichspräzision (Gauge R&R)
Hier geht es um die Wiederhol- und Vergleichspräzision (Repeatability & Reproducibility) der Messeinrichtung (Gauge). Die Prüfung kommt zur Anwendung, wenn das Messmittel nach Verfahren 1 bereits als fähig eingestuft worden ist.
Ist der Benutzer in die Messung mit eingebunden, etwa bei manuellen Messungen, wird das Verfahren 2 eingesetzt. Hierbei werden mindestens zehn ausgesuchte und markierte Serienteile, die möglichst den gesamten Streubereich des Merkmals abdecken sollten, von mindestens drei Prüfern mindestens je zweimal in zufälliger Reihenfolge vermessen. Die Markierungen der Teile dürfen dabei den Prüfpersonen nicht bekannt sein und diese dürfen die Ergebnisse der anderen Prüfpersonen nicht kennen.
Werden die Messungen automatisch vorgenommen, so sind diese in der Regel unabhängig vom Einfluss der Benutzer, so dass das Verfahren 3 greift, das eine Variante des Verfahrens 2 ist. Dies ist für AOIs generell der Fall. Dabei werden mindestens 25 ausgesuchte und markierte Serienteile mindestens zweimal in randomisierter Reihenfolge vermessen.
Wichtig ist, dass die Teile auch tatsächlich wiederholt vermessen werden können und dass sie sorgfältig für spätere Vergleichsmessungen verwahrt werden.
Nach Abschluss der Messungen werden im Verfahren 2 und 3 für alle Messreihen der Mittelwert, die Standardabweichung und die Spannweite berechnet, also die Differenz aus dem größten und kleinsten Messwert. Daraus werden Fähigkeitsindizes %GRR berechnet, welche die Bedeutung Präzision/Toleranz haben. Eine detaillierte Darstellung der statistischen Details würde hier den Rahmen sprengen. Die Messeinrichtung ist für %GRR≤10 fähig, für 10≤%GRR<30 bedingt fähig und sonst nicht fähig.
Verfahren 4: Linearität, Verfahren 5: Stabilität und Drift, Verfahren 6: diskrete Merkmale
Die Prüfung der Linearität spielt für die MSA von AOIs eine untergeordnete Rolle. Die im Verfahren 5 definierten Maßnahmen betreffen nicht direkt die MSA, sondern die periodische Sicherstellung der Fähigkeit der Mess- und Prüfeinrichtungen durch den Betreiber. Verfahren 6 ähnelt dem Verfahren 7, das für AOIs die passendere Alternative ist.
Verfahren 7: Nachweis der Prüfprozessfähigkeit anhand diskreter Merkmale
Das Verfahren wird angewendet, wenn durch das AOI diskrete Attribute ermittelt werden, die auf die Kategorisierung „gut“ oder „schlecht“ ohne Angabe von Messwerten hinauslaufen. Evtl. kann noch eine dritte Kategorie, beispielweise „Nacharbeiten“ hinzukommen. Die Merkmale können entweder ohne Messung kontinuierlicher Größe klassifiziert werden, Beispiele sind etwa „Bauteil ist vom Typ A / Bauteil ist vom Typ B“ oder „Bohrung vorhanden / Bohrung nicht vorhanden“. Genauso sind aber auch aus internen Messungen folgende Attribute möglich, wobei diese dann „innerhalb des Toleranzbereichs“ bzw. „außerhalb des Toleranzbereichs“ lauten.
Für die Prüfung werden Referenzteile verwendet, von denen üblicherweise die Hälfte Gutteile sind und die Hälfte Fehlerteile. Die Merkmalswerte der Referenzteile müssen vorab ermittelt und dokumentiert werden. Die Kennzeichnung der Referenzteile muss so erfolgen, dass sie durch autorisiertes Personal lesbar ist, durch die Bedienpersonen jedoch nicht. Möglichkeiten dazu sind QR-Codes oder Barcodes etc. Bei diskreten Attributen ist ein Vergleichsstandard, beispielsweise ein Grenzmusterkatalog erforderlich, gegen den die Prüfobjekte verglichen werden. Dies können foto-grafische Abbildungen sein, aber auch eine Sammlung existierender Teile mit entsprechenden Eigenschaften.
Bei kontinuierlichen Merkmalswerten besteht die Schwierigkeit, dass diese auf unabhängige Art und Weise genauer gemessen werden müssen, als die zu prüfende Anlage dies könnte. Die zugehörigen Messunsicherheiten müssen also bekannt sein und es muss sichergestellt sein, dass tatsächlich alle Referenzteile um eine erweiterte Messunsicherheit für Gutteile innerhalb und für Fehlerteile außerhalb des Toleranzbereichs liegen. Dabei soll der gesamte Bereich von deutlich unterhalb des UGW und deutlich oberhalb des OGW abgedeckt werden. Als erweiterte Messunsicherheit wählt man dabei die mit dem Faktor zwei oder drei multiplizierte Messunsicherheit.
Das Los der Referenzteile sollte möglichst groß sein, mindestens aber 50 Teile umfassen und es sind mindestens zwei Prüfdurchgänge erforderlich.
Können die Bewertungen durch das Prüfpersonal beeinflusst werden, müssen die Referenzteile jeweils in mindestens zwei Prüfdurchläufen von mindestens drei Prüfern unabhängig voneinander beurteilt werden. Ist der Einfluss der Prüfer ausgeschlossen, wovon man bei automatisierten Systemen ausgeht, müssen die Referenzteile in mindestens 6 Durchläufen geprüft werden. Die Reihenfolge der Prüfobjekte ist in beiden Fällen für jeden Prüfdurchlauf nach dem Zufallsprinzip neu zu wählen.
Für jeden Durchlauf wird gezählt, in wie vielen Fällen das Ergebnis des Prüfgeräts mit dem Sollwert übereinstimmt. Der resultierende Fähigkeitsindex κ (Kappa) ist die Anzahl der Übereinstimmungen dividiert durch die Anzahl der geprüften Referenzteile. Für κ=1 wurden also sämtliche Teile korrekt klassifiziert.
Man verlangt für den Fähigkeitsnachweis κ=0.9, wenn das Ergebnis durch das Prüfpersonal beeinflusst werden kann und κ=1 für automatische Systeme. Für niedrigere Kappawerte bis κ>0.7 ist das Prüfsystem bedingt fähig und für κ<0.7 nicht fähig.
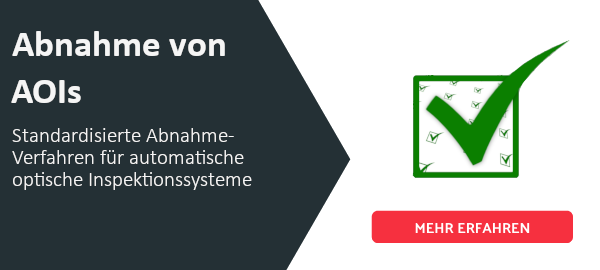